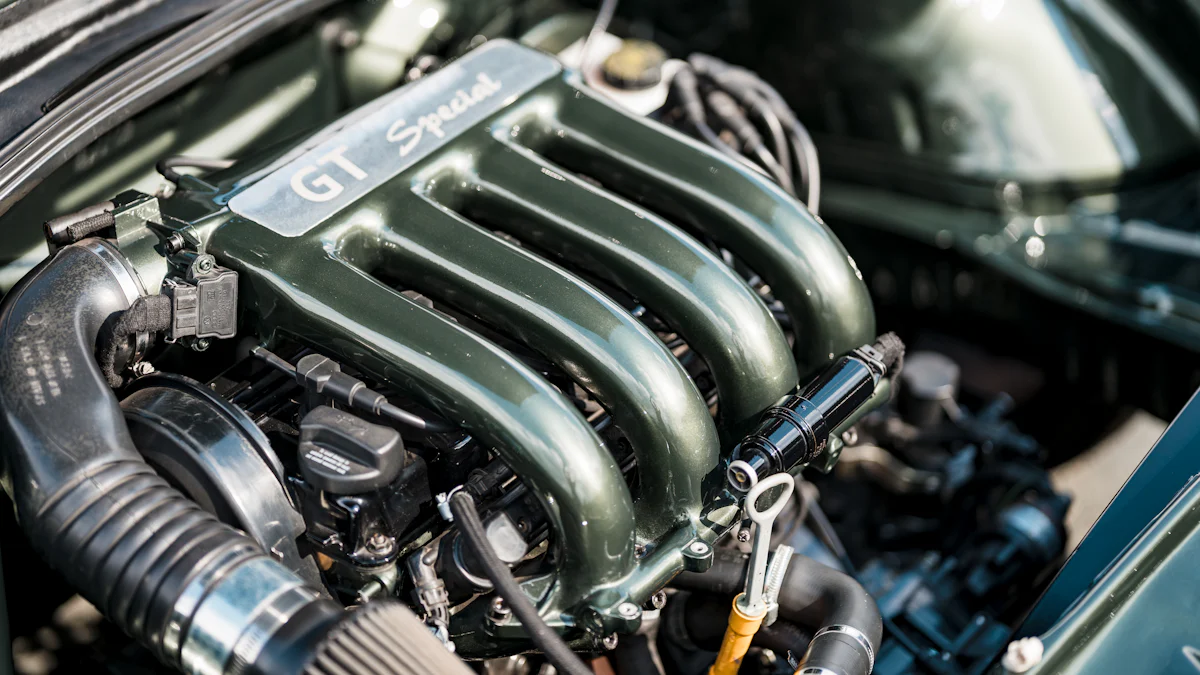
The intake manifold plays a crucial role in an engine’s performance. This component directs the air-fuel mixture from the throttle body to the cylinder head. Proper distribution of this mixture ensures optimal combustion efficiency. Dyno testing has shown that a stock intake manifold can produce 381 torque and 339 horsepower. Such performance highlights the importance of this component in achieving high engine output. The intake manifold’s design and material significantly impact airflow dynamics, which directly influences horsepower and torque.
Understanding Intake Manifolds
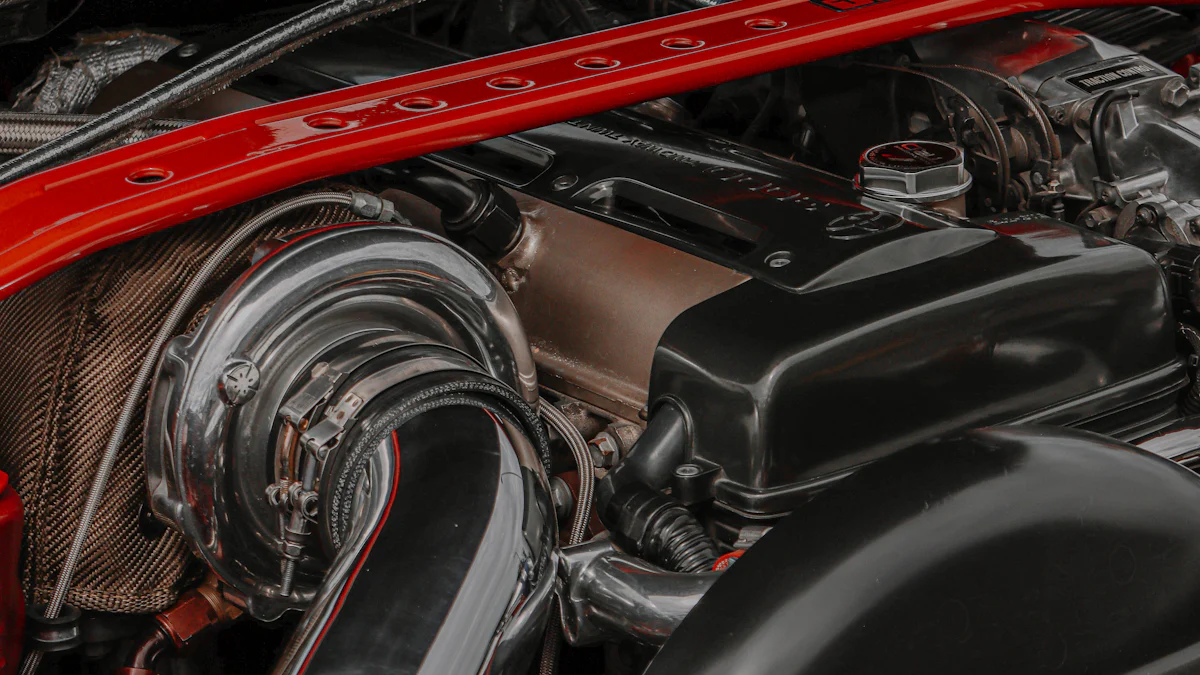
Definition and Purpose
What is an Intake Manifold?
An intake manifold serves as a critical component in an internal combustion engine. This manifold directs the air-fuel mixture from the throttle body to the cylinder head. The design of the intake manifold ensures that each cylinder receives an equal amount of the mixture. This distribution promotes efficient combustion.
Purpose of an Intake Manifold in an Engine
The intake manifold’s primary purpose involves optimizing engine performance. By evenly distributing the air-fuel mixture, the manifold enhances combustion efficiency. This efficiency translates to improved horsepower and torque. Properly functioning intake manifolds contribute to smoother engine operation and better fuel economy.
Types of Intake Manifolds
Single Plane Manifolds
Single plane manifolds feature a single plenum chamber. This design allows for high RPM performance. The single plane manifold offers less resistance to airflow. This characteristic makes it suitable for racing applications where maximum power at high RPM is essential.
Dual Plane Manifolds
Dual plane manifolds contain two separate plenum chambers. This design improves low to mid-range RPM performance. The dual plane manifold provides better fuel distribution at lower speeds. This type of manifold is ideal for street-driven vehicles requiring a balance of power and drivability.
Individual Throttle Bodies (ITBs)
Individual Throttle Bodies (ITBs) offer a unique approach to air-fuel mixture distribution. Each cylinder has its own throttle body. This configuration allows for precise control over the air entering each cylinder. ITBs enhance throttle response and overall engine performance. High-performance and racing engines often use ITBs for their superior airflow characteristics.
Materials and Construction
Common Materials Used
Manufacturers commonly use aluminum for intake manifolds. Aluminum offers a good balance of strength and weight. Some intake manifolds use composite materials. These materials provide excellent thermal insulation properties. Composite intake manifolds help maintain cooler air temperatures, improving combustion efficiency.
Manufacturing Processes
The manufacturing process for intake manifolds involves several steps. Casting remains the most common method for producing aluminum intake manifolds. This process involves pouring molten aluminum into a mold. After cooling, the manifold undergoes machining to achieve precise dimensions. Composite intake manifolds often use injection molding. This process involves injecting molten material into a mold under high pressure. Both methods ensure the intake manifold meets strict performance and durability standards.
How Intake Manifolds Work
Air-Fuel Mixture Distribution
Role in Air-Fuel Ratio
The intake manifold plays a crucial role in maintaining the air-fuel ratio. This ratio determines how much air mixes with fuel before combustion. An optimal air-fuel ratio ensures efficient engine performance. The intake manifold distributes the mixture evenly to each cylinder. This even distribution helps maintain the desired ratio across all cylinders.
Impact on Combustion Efficiency
Combustion efficiency directly impacts engine performance. The intake manifold ensures that each cylinder receives an equal amount of the air-fuel mixture. This equal distribution promotes complete combustion. Complete combustion leads to better fuel efficiency and more power output. Properly designed intake manifolds enhance overall engine efficiency.
Airflow Dynamics
Design Considerations
Intake manifold design significantly affects airflow dynamics. Engineers consider factors like plenum volume and runner length. Plenum volume influences the amount of air available for combustion. Runner length affects how quickly air reaches the cylinders. Different designs optimize for specific RPM ranges. High-revving engines benefit from shorter runners, while low-end torque requires longer runners.
Impact on Engine Performance
Airflow dynamics directly influence engine performance. A well-designed intake manifold improves airflow to the cylinders. Improved airflow results in better combustion and increased power. The material of the intake manifold also affects performance. Aluminum and composite materials offer different thermal properties. These properties impact how air flows through the manifold. Efficient airflow dynamics contribute to higher horsepower and torque.
Integration with Other Engine Components
Connection to Throttle Body
The intake manifold connects directly to the throttle body. The throttle body controls the amount of air entering the engine. When the throttle opens, air flows through the intake manifold. The manifold then distributes this air to each cylinder. A seamless connection between these components ensures smooth engine operation. Any restriction in this pathway can reduce engine performance.
Interaction with Fuel Injectors
Fuel injectors play a vital role in the air-fuel mixture. The intake manifold works closely with these injectors. Injectors spray fuel into the intake manifold. The manifold then mixes this fuel with incoming air. Proper interaction between these components ensures an optimal air-fuel mixture. This interaction is crucial for achieving efficient combustion. Faulty injectors or manifold issues can disrupt this balance.
Common Issues with Intake Manifolds
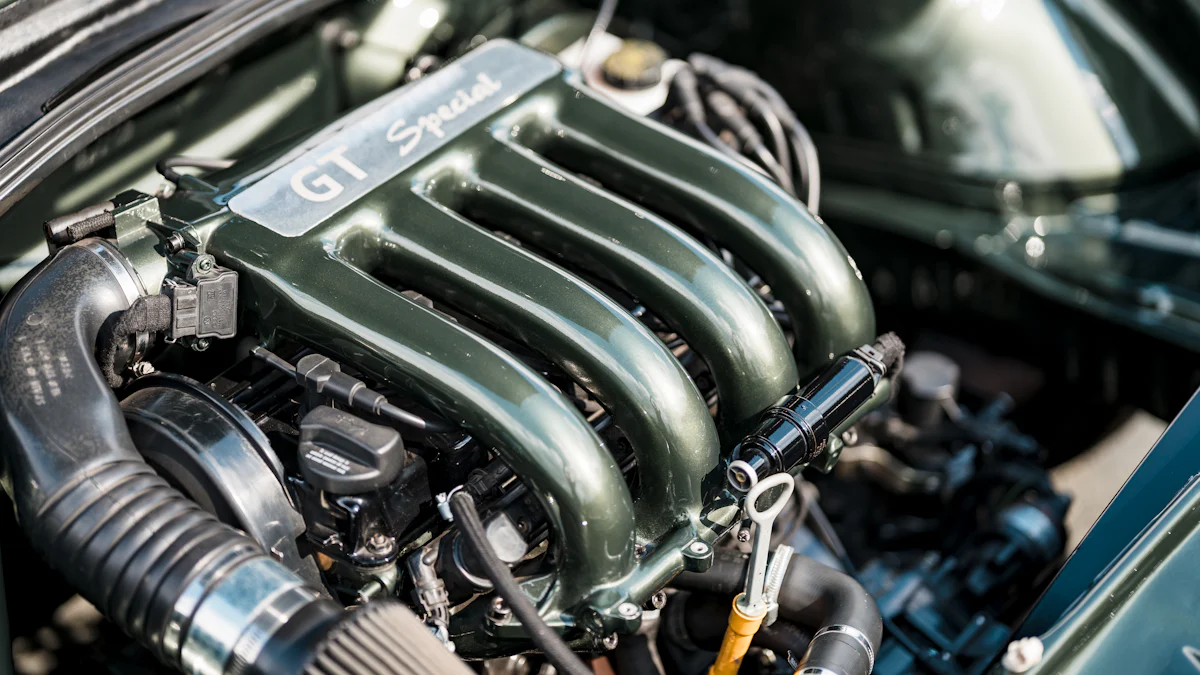
Symptoms of a Faulty Intake Manifold
Engine Misfires
Engine misfires often indicate a faulty intake manifold. Misfires occur when the air-fuel mixture does not ignite properly in the cylinder. An uneven distribution of the air-fuel mixture can cause this issue. A damaged intake manifold disrupts this distribution, leading to misfires. Misfires result in rough engine operation and reduced performance.
Reduced Fuel Efficiency
Reduced fuel efficiency serves as another symptom of a problematic intake manifold. A malfunctioning manifold affects the air-fuel ratio. This imbalance leads to incomplete combustion. Incomplete combustion wastes fuel, lowering overall efficiency. Drivers may notice increased fuel consumption and higher emissions.
Causes of Intake Manifold Problems
Wear and Tear
Wear and tear contribute significantly to intake manifold problems. Over time, the manifold experiences stress from heat and pressure. These factors cause the material to degrade. Cracks and leaks develop, disrupting the air-fuel mixture. Regular maintenance helps identify wear before it causes severe issues.
Manufacturing Defects
Manufacturing defects also lead to intake manifold problems. Poor-quality materials or flawed production processes result in weak manifolds. These defects manifest as cracks or improper sealing surfaces. Defective manifolds fail to distribute the air-fuel mixture evenly. Identifying these issues early prevents long-term damage to the engine.
Diagnosing Intake Manifold Issues
Visual Inspection
Visual inspection remains a primary method for diagnosing intake manifold issues. Inspectors look for visible cracks, leaks, or signs of wear. A thorough examination includes checking the manifold’s connections to other components. Any visible damage indicates the need for further investigation or repair.
Diagnostic Tools
Diagnostic tools provide more precise methods for identifying intake manifold problems. Mechanics use tools like smoke machines to detect leaks. Pressure tests reveal weaknesses in the manifold structure. Advanced diagnostic equipment measures airflow and fuel distribution. These tools offer accurate assessments, guiding effective repairs.
Solutions and Maintenance
Repairing Intake Manifolds
Common Repair Techniques
Repairing an intake manifold involves several techniques. Mechanics often use epoxy to seal small cracks or leaks. This method provides a temporary fix but may not last long under high pressure. Welding offers a more permanent solution for aluminum intake manifolds. The welding process requires skill to avoid further damage. For composite intake manifolds, specialized adhesives can repair minor damages. These adhesives maintain the structural integrity of the manifold.
When to Replace vs. Repair
Deciding whether to replace or repair an intake manifold depends on the extent of the damage. Minor cracks and leaks can often be repaired effectively. However, extensive damage or multiple issues may necessitate a replacement. A new intake manifold ensures optimal performance and reliability. Regular inspections help identify when a repair is no longer sufficient. Replacement becomes essential to maintain engine efficiency and prevent further damage.
Preventative Maintenance
Regular Inspections
Regular inspections play a crucial role in maintaining an intake manifold. Visual checks can identify early signs of wear and tear. Inspectors should look for cracks, leaks, and loose connections. Regular inspections help catch issues before they escalate. This proactive approach extends the lifespan of the intake manifold. Mechanics recommend scheduling inspections during routine maintenance.
Cleaning and Upkeep
Proper cleaning and upkeep are vital for an intake manifold’s performance. A dirty intake manifold can allow harmful particles into the engine. These particles cause significant damage over time. Cleaning involves removing carbon deposits and other contaminants. Specialized cleaners designed for intake manifolds provide the best results. Regular cleaning ensures optimal airflow and combustion efficiency. Just Diesel Performance emphasizes the importance of clean intake manifolds for engine performance and efficiency.
“It is important to clean your intake manifold properly, as the air it provides your engine is key to performance, economy, and efficiency. A dirty intake manifold can also allow harmful particles into your engine, potentially causing untold, irreparable damage.” — Just Diesel Performance
Upgrading Intake Manifolds
Performance Benefits
Upgrading an intake manifold offers several performance benefits. High-performance intake manifolds improve airflow to the engine. Improved airflow results in increased horsepower and torque. Upgraded manifolds often feature advanced designs that optimize air-fuel mixture distribution. Performance enthusiasts notice significant gains in engine responsiveness and power output. Upgrades also enhance the overall driving experience.
Considerations for Upgrades
Several factors should be considered when upgrading an intake manifold. Compatibility with the engine type is crucial. Not all intake manifolds fit every engine. Material and design also play a significant role. Aluminum and composite materials offer different benefits. Aluminum provides durability, while composites offer better thermal insulation. The intended use of the vehicle influences the choice of intake manifold. Racing applications require different specifications than street-driven vehicles. Proper research ensures the selected upgrade meets performance goals.
Intake manifolds play a pivotal role in engine performance. Proper air-fuel mixture distribution ensures efficient combustion, leading to enhanced horsepower and torque. Key points discussed include the various types of intake manifolds, their materials, and construction methods. Regular maintenance, such as cleaning and inspections, prevents issues like vacuum leaks and ensures optimal engine efficiency. Upgrading to high-performance intake manifolds can significantly boost engine output. Maintaining and optimizing intake manifolds is essential for achieving peak engine performance and longevity.
Post time: Jul-24-2024